
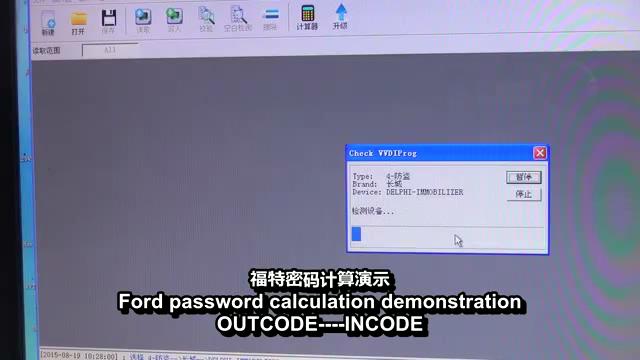
Second to allow the ASIC to function even if one cell is open/shorted. One to dampen any voltage spikes above 6.2 volts.
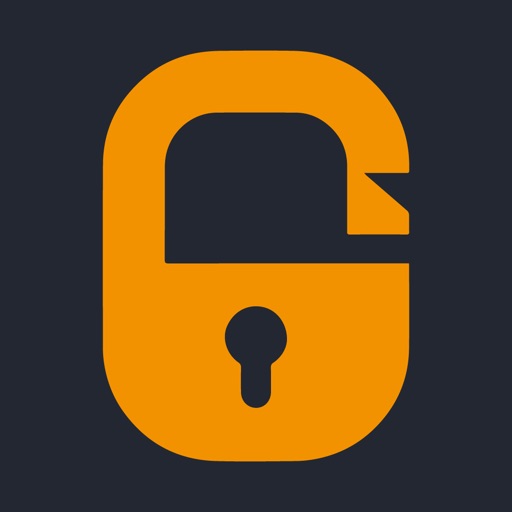
I am guessing that the zener diodes on the inputs serve two functions. There is a clear insulating over coating on this section to prevent any leakage that could result in a catastrophic failure of the board. It gets its power from the four cells it is monitoring and only has a single input signal from its neighbor which with a zener diode is prevent from going negative.Īll this isolation is required because the full battery voltage of up to 393 volts is being monitored on a standard circuit board. The output of that photocoupler is looped through the first 12 ASICs then another photocoupler then 12 more ASICs and finally through the last photocoupler back to the RISC processors input UART.Įach ASIC is actually an island onto itself. Communications with the ASICs is through a serial link starting with a UART pin on the RISC processor and going through the first photocoupler. The most interesting part is that the custom ASIC part is coupled to the first section through three photocouplers.
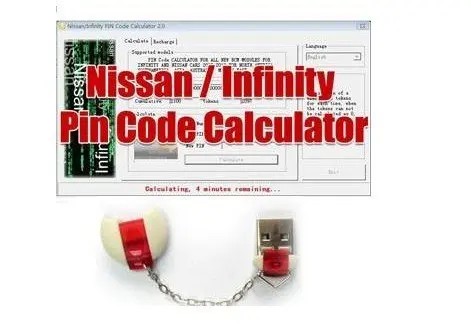
This is the section I have been looking into in detail. The second section is almost totally isolated from the first and consists of 24 custom ASICs that monitor the 96 cell pairs. This is the part that Leaf Spy communicates with to get battery voltages and shunt settings. The first section is common to all ECUs in the Leaf with a CAN interface and RISC processor. To me it is all new but I though it could be useful to others to know more about the inner working of the battery balancing circuits and how it interfaces with the Leaf. This is the first time I have looked into a battery controller so some of what I say may be common knowledge.
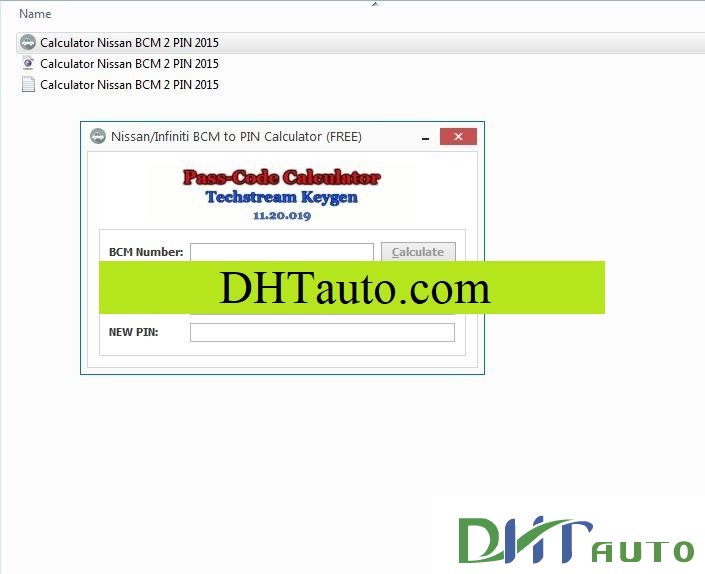
I was fortunate enough to be loaned a BMS board that had been burnt out while trying to converted a Leaf battery pack into a 4 x 100 volt configuration for use in another vehicle.
